Compressive strength of concrete: Out of many test applied to the concrete, this is the utmost important which gives an idea about all the characteristics of concrete. By this single test one judge that whether Concreting has been done properly or not.
For cube test two types of specimens either cubes of 15 cm X 15 cm X 15 cm or 10cm X 10 cm x 10 cm depending upon the size of aggregate are used. For most of the works cubical moulds of size 15 cm x 15cm x 15 cm are commonly used.
Dimension, tolerance and materials of 150 mm cube mould.
Dimension, tolerance and materials of 150 mm cube mould.
S.No.
|
Description
|
Requirements
|
1
| Distance between opposite faces, mm |
150 ± 0.2
|
2
| Height of mould, mm |
150 ± 0.2
|
3
| Thickness of wall plate, mm |
8
|
4
| Angle between adjacent interior faces and between interior faces and top and bottom plates of mould. |
90 ± 0.50
|
5
| Length of base plate, mm |
280
|
6
| Width of base plate, mm |
215
|
7
| Thickness of base plate, mm |
8
|
8
| Permissible variation in the planeness of interior faces:
for new moulds, mm
for moulds in use, mm
|
0.03
0.05
|
9
| Permissible variation in the planeness of base plate, mm |
0.03
|
10
| materials a) Side plate b) Base plate |
Cast iron
Cast iron
|
TAMPING ROD
As per IS:10086-1982, the tamping rod shall be 16±0.5 mm dia and 600±2 mm long with a rounded working end and shall be made of mild steel.
As per IS:10086-1982, the tamping rod shall be 16±0.5 mm dia and 600±2 mm long with a rounded working end and shall be made of mild steel.
Note:- For aggregates larger than 38 mm, bigger than 150 mm moulds are to be used. See IS:10086-1982
CASTING OF CUBES:
The cube mould plates should be removed, properly cleaned assembled and all the bolts should be fully tight. A thin layer of oil then shall be applied on all the faces of the mould. It is important that cube side faces must be parallel.
The cube mould plates should be removed, properly cleaned assembled and all the bolts should be fully tight. A thin layer of oil then shall be applied on all the faces of the mould. It is important that cube side faces must be parallel.
After taking concrete samples and mixing them, the cubes shall be cast as soon as possible. The concrete sample shall be filled into the cube moulds in layers approximately 5 cm deep. In placing each scoopful of concrete, the scoop shall be moved around the top edge of the mould as the concrete slides from it, in order to ensure a symmetrical distribution of the concrete with in the mould. Each layer shall be compacted either by hand or by the vibration as described below.
COMPACTION BY HAND:
Each layer of the concrete filled in the mould shall be compacted by not less than 35 strokes by tamping bar. The strokes shall be penetrate into the underlying layer and the bottom layer shall be rodded throught its depth. Where voids are left by the tamping bar the sides of the mould shall be tapped to close the voids.
Each layer of the concrete filled in the mould shall be compacted by not less than 35 strokes by tamping bar. The strokes shall be penetrate into the underlying layer and the bottom layer shall be rodded throught its depth. Where voids are left by the tamping bar the sides of the mould shall be tapped to close the voids.
COMPACTION BY VIBRATION:
When compacting by vibration each layer shall be vibrated by means of an electric or pneumatic hammer or vibrator or by means of a suitable vibrating table until the specified condition is attained.
When compacting by vibration each layer shall be vibrated by means of an electric or pneumatic hammer or vibrator or by means of a suitable vibrating table until the specified condition is attained.
CURING :
The casted cubes shall be stored under shed at a place free from the vibration at a temperature 220C to 330C for 24 hours covered with wet straw or gunny sacking.
The casted cubes shall be stored under shed at a place free from the vibration at a temperature 220C to 330C for 24 hours covered with wet straw or gunny sacking.
The cube shall be removed from the moulds at the end of 24 hours and immersed in clean water at a temperature 240C to 300C till the 7 or 28-days age of testing. The cubes shall be tested in the saturated and surface dry condition.
For the true representation of actual strength of concrete in the structure, extra cubes shall be cast, stored and curded as per the identical conditions of that structure, and tested at required age.
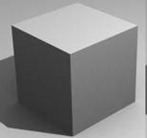
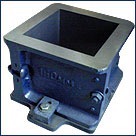
This concrete is poured in the mould and tempered properly so as not to have any voids. After 24 hours these moulds are removed and test specimens are put in water for curing. The top surface of these specimen should be made even and smooth. This is done by putting cement paste and spreading smoothly on whole area of specimen.
These specimens are tested by compression testing machine after 7 days curing or 28 days curing. Load should be applied gradually at the rate of 140 kg/cm2 per minute till the Specimens fails. Load at the failure divided by area of specimen gives the compressive strength of concrete.
Following are the procedure for Compressive strength test of Concrete Cubes
APPARATUS
Compression testing machine
PREPARATION OF CUBE SPECIMENS
The proportion and material for making these test specimens are from the same concrete used in the field.
SPECIMEN
6 cubes of 15 cm size Mix. M15 or above
MIXING
Mix the concrete either by hand or in a laboratory batch mixer
HAND MIXING
(i)Mix the cement and fine aggregate on a water tight none-absorbent platform until the mixture is thoroughly blended and is of uniform color
(ii)Add the coarse aggregate and mix with cement and fine aggregate until the coarse aggregate is uniformly distributed throughout the batch
(iii)Add water and mix it until the concrete appears to be homogeneous and of the desired consistency
SAMPLING
(i) Clean the mounds and apply oil
(ii) Fill the concrete in the molds in layers approximately 5cm thick
(iii) Compact each layer with not less than 35strokes per layer using a tamping rod (steel bar 16mm diameter and 60cm long, bullet pointed at lower end)
(iv) Level the top surface and smoothen it with a trowel
CURING
The test specimens are stored in moist air for 24hours and after this period the specimens are marked and removed from the molds and kept submerged in clear fresh water until taken out prior to test.
PRECAUTIONS
The water for curing should be tested every 7days and the temperature of water must be at 27+-2oC.
PROCEDURE
(I) Remove the specimen from water after specified curing time and wipe out excess water from the surface.
(II) Take the dimension of the specimen to the nearest 0.2m
(III) Clean the bearing surface of the testing machine
(IV) Place the specimen in the machine in such a manner that the load shall be applied to the opposite sides of the cube cast.
(V) Align the specimen centrally on the base plate of the machine.
(VI) Rotate the movable portion gently by hand so that it touches the top surface of the specimen.
(VII) Apply the load gradually without shock and continuously at the rate of 140kg/cm2/minute till the specimen fails
(VIII) Record the maximum load and note any unusual features in the type of failure.
NOTE
Minimum three specimens should be tested at each selected age. If strength of any specimen varies by more than 15 per cent of average strength, results of such specimen should be rejected. Average of there specimens gives the crushing strength of concrete. The strength requirements of concrete.
CALCULATIONS
Size of the cube =15cm x15cm x15cm
Area of the specimen (calculated from the mean size of the specimen )=225cm2
Characteristic compressive strength(f ck)at 7 days =
Expected maximum load =fck x area x f.s
Range to be selected is …………………..
Similar calculation should be done for 28 day compressive strength
Maximum load applied =……….tones = ………….N
Compressive strength = (Load in N/ Area in mm2)=……………N/mm2
=……………………….N/mm2
REPORT
a) Identification mark
b) Date of test
c) Age of specimen
d) Curing conditions, including date of manufacture of specimen
f) Appearance of fractured faces of concrete and the type of fracture if they are unusual
RESULT
Average compressive strength of the concrete cube = ………….N/ mm2 (at 7 days)
Average compressive strength of the concrete cube =………. N/mm2 (at 28 days)
Percentage strength of concrete at various ages:
The strength of concrete increases with age. Table shows the strength of concrete at different ages in comparison with the strength at 28 days after casting.
Age
|
Strength per cent
|
1 day
|
16%
|
3 days
|
40%
|
7 days
|
65%
|
14 days
|
90%
|
28 days
|
99%
|
Compressive strength of different grades of concrete at 7 and 28 days
Grade of Concrete
|
Minimum compressive strength N/mm2 at 7 days
|
Specified characteristic compressive strength (N/mm2) at 28 days
|
M15
|
10
|
15
|
M20
|
13.5
|
20
|
M25
|
17
|
25
|
M30
|
20
|
30
|
M35
|
23.5
|
35
|
M40
|
27
|
40
|
M45
|
30
|
45
|